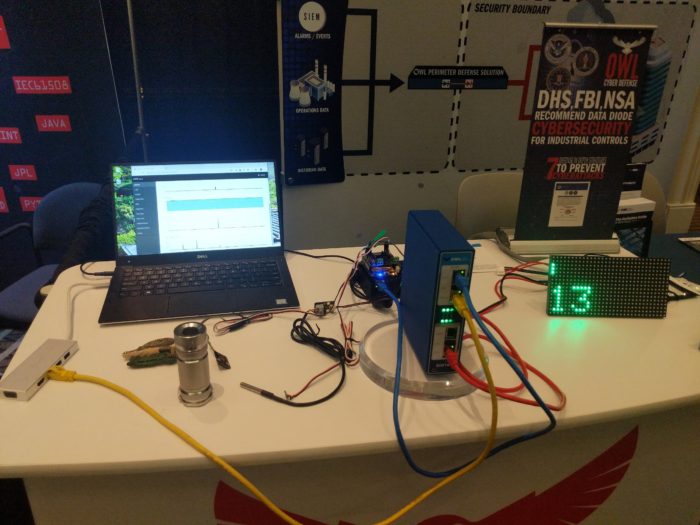
At the end of last year, one of our product managers heard about my bioreactor demo. He thought it would be great to have something similar for software he was getting ready to launch for his product.
The software (used on our other data diodes) lets one set up Modbus registers to be read by the client on one side of the data diode and then set up the server on the other side of the diode to be read by a Modbus client.
Due to the holidays, we only were able to get together to talk about it mid-January, and then he told me he wanted something to show at an event at the end of February. So time was already getting tight, not to mention the time it took for him to get approval for the funds and the project.
In the end, I had about two weeks to design, build, test, and deliver something.
Catching the Modbus
The software was to provide Modbus compatibility for our DiOTa, the smallest of our data diodes. This was a big deal, as a lot of organizations were interested in using the DiOTa with Modbus across their critical infrastructure networks.
The hardware I was building was to provide a server and client to flank the diode. But principally, it was to be much more attractive, engaging, and interactive than the usual tablets and interfaces we have traditionally used to demonstrate our software and hardware.
I knew nothing about the technical underpinnings of Modbus when we started, but luckily there was an Arduino library. And, while I wanted an excuse to use new boards, we decided to reuse as much of my bioreactor set up as possible.
So, in about a week, I ordered what I needed, leveled up on Modbus, and built a fun set up for the product manager.
Mix of new and old
The library would not run on my Uno (the Uno barely had the memory for it), so I purchased two Adafruit Metro M4s. One would be the client and one would be the server. I went with the Metro as we had one Arduino Ethernet shield already and an I/O shield we could easily use to connect some of the sensors we had, so we stuck to the Arduino form factor (I so wanted to use a Feather).
I also wanted something with flash, so we decided to get an LED Matrix and Matrix Shield to show the data as it was read by the Modbus client stack (alas, the matrix shield needs so many pins, that we couldn’t put it on the server stack). On the server stack we added a battery shield, as we were initially planning to make the demo in a power distribution theme.
And, in a total impulse buy while perusing the shelves at Microcenter (always a bad thing), I picked up a dirt cheap light sensor (and smaller than a pinky fingernail!).
Keep in mind, the time constraint was a major driver in what we chose to use for the build.
We ended up with a temperature sensor, a magnet sensor (to simulate opening and closing of a coil), and a light sensor. We were also sending across to the client the uptime of the server and the battery voltage of the battery shield. Most of this changed dynamically – holding the temp sensor to raise temp, placing or removing a magnet from the magnet sensor, flashing light or covering the light sensor, and turning off or on the main power to go onto battery power.
Fun stuff.
And she said, and she said
I had it up and running in about a week (nights and weekends style, as building this was not part of my usual role at the company – the bioreactor was). I then headed down to the office to train folks on how to use it and see how well it worked with the data diode.
All went swimingly and we were all thrilled to see the sensor data updating at the client across the data diode.
Turns out that our head of training saw the demo setup and saw the value of the demo for training.
Then a few sales guys saw it and asked to use it for client demos.
This thing had legs!
Screeching halt, sort of
While the bioreactor was all for me, this was the first time I had to build something for someone else in the company. The build was also a test of the idea of using readily available maker hardware to help explain a concept. Basically, turning a technical demo into a more tangible experience, which I’d like to explore further.
Alas, soon after the product manager returned from showing the set up at his event (photo above – good feedback, too) the whole world shut down and I have not been able to modify the demo or make extra ones (such as for training or sales) or explore other demos. All discussions of tangible experiences has sort of died down.
Oh well. The project was fast and fun. And I’m itching to get another commission.
In any case, I haven’t stopped exploring other ways to show concepts in tangible ways, like a physical narrative of the digital, or something like that.
And that’s a story for another post.